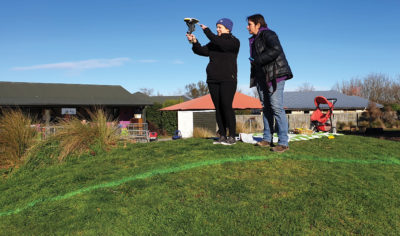
In this example of “centimeters everywhere for everyone,” two preschool mothers use augmented reality to mark out a green line showing where a road proposed by the city would alter the land of their school. They are unaware they are using RTK enabled by Trimble’s VRS Now service.
In this exhilarating age of self-driving cars, we must flip, flip, flip the calendar back three decades to fully appreciate the role of three-dimensional, centimeter-accurate kinematic positioning in real time, or Real Time Kinematic (RTK), in the autonomous vehicle revolution we are seeing today.
It was at that time, in the early 1990s, when private industry began building on a foundation of RTK development breakthroughs to make hardware and software improvements enabling widespread commercial uses in marine, surveying, mining and construction.
By 1993, the U.S. Army Corps of Engineers had completed a successful multi-year project to develop a complete operational prototype RTK system to vastly improve the economies, accuracies and timeliness of dredging and hydrographic surveying. The effort led to a pivotal patent by Benjamin W. Remondi, a GPS technologist for the National Geodetic Survey (NGS). (See RTK – Part 3.)
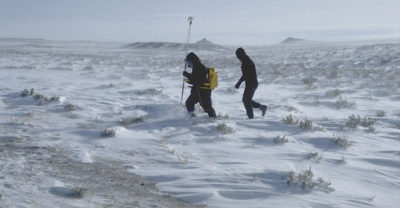
Carl Sumpter of the U.S. Forest Service tests RTK for cadastral survey in Wyoming in 1993, part of a demonstration by Nichols, walking behind. Source: Mark Nichols.
Soon, the technology was being implemented in other applications:
- By summer 1993, the Corps was using the system on photogrammetric aircraft under a cooperative research and development agreement with Photo Science Inc. (now Fugro EarthData) to reduce or replace ground control for photogrammetric mapping. The National Oceanic and Atmospheric Association (NOAA) was a key partner in this work, and Ashtech on-the-fly (OTF) processing software was used (although not in real time), and is described in “The Development of GPS Controlled Photogrammetry within the Corps of Engineers.”
- Also in 1993, the Corps signed a cooperative research and development agreement with Caterpillar, which was developing computer-aided earthmoving systems, to put OTF-RTK on board their equipment. Later that year, Caterpillar and the Corps tested the prototype, described in “Construction Vehicle Navigation and Automation,” by Jeffrey Walker, and Caterpillar entered an agreement in 1994 with Trimble for production development.
Not coincidentally, RTK commercialization took off like a rocket at this time, with Trimble, Ashtech, Leica and other companies creating products focused on form factor and process improvements. Did these RTK pioneers from the Corps, academia, science and private industry see a multibillion-dollar industry forming on the horizon?
“No—and anybody who would say so is fooling you,” said Bryn Fosburgh, senior vice president at Trimble, who as a young engineer worked on the Corps’ RTK development project.
Putting the crystal ball aside, the early RTK innovators believed strongly in the potential of the technology to solve costly problems of positional accuracy in marine and land surveying environments and civil construction and agriculture. It was their dogged persistence that birthed what is today considered a utility feeding countless positioning-centric applications.
In this fourth article on the history of RTK, we wrap up the series with a focus on early RTK commercialization in different applications, and Trimble’s role in expanding the potential of the technology to give surveyors and geospatial professionals capabilities they didn’t even know they wanted.
Trimble releases first RTK commercial product
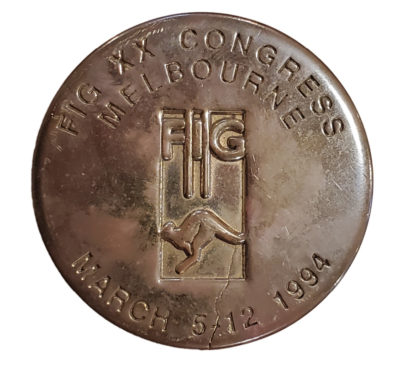
A brass disk from the 1994 International Federation of Surveyors conference in Melbourne. Source: Steve DeLoach
In 1990, Trimble became the first publicly traded GPS company, and at the same time, dedicated itself to developing products that used the constellation of satellites known as the Global Positioning System, or GPS.
As part of its leveraging of GPS, Trimble developed RTK surveying products in two phases, enabling customers to come on the journey and learn about the technology before OTF positioning was solved in a commercially available product.
In 1993, Trimble released its first commercial RTK product, called the Site Surveyor system, described in the ION paper “Centimeters in the Field, a User’s Perspective of Real-Time Kinematic Positioning in a Production Environment,” by Nick Talbot, a fellow and senior software engineer with Trimble’s GNSS (Global Navigation Satellite System) Algorithms Group. The system required static initialization using a known baseline, or an initializer plate. The hardware was backpack-mounted, required a separate radio datalink, and was bulky compared to later generations of products. But even with its weight and ergonomic limitations, surveyors quickly saw the advantage of obtaining results in the field rather than logging data and post-processing it back in the office.
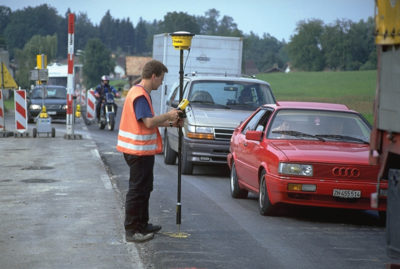
The Trimble 4800 offered one of the first “smart antenna” RTK systems where the GPS, radio and antenna were built into one unit with batteries in the pole and no backpack required. Source: Trimble
Early interest in the technology came from mining and forestry. In February of 1993, Mark Nichols, general manager at Trimble and one of the company’s early RTK development leaders, demonstrated the RTK system to two customers. One was Carl Sumpter of the U.S. Forest Service, testing RTK for cadastral survey in Wyoming in February. In a photo of the demonstration, Nichols, who is from New Zealand, is shown walking behind Sumpter “in my best Kiwi ski gear. Ideal terrain for RTK—not a tree or obstruction in sight, so no danger of loss of lock.” Jim Long of Carter Mining Company was the other customer. “We demonstrated RTK GPS to him in the mine,” Nichols said, “and he was the first customer to buy it.”
OTF untethers the user
Around this time, private companies and individuals worked on the same idea for commercialization of RTK, but Trimble had a head start of about two years on the competition and added OTF capabilities and testing internally in late 1993.
In March 1994, Trimble released its first commercial RTK receiver with OTF capabilities, described in patent “Centimeter accurate global positioning system receiver for on-the-fly real-time kinematic measurement and control,” at the International Federation of Surveyors (FIG) conference in Melbourne, Australia. The system had a dual frequency antenna developed to operate without the 16-inch ground plane used for static surveying to reduce multipath.
Talbot remembers the breakthrough moment when the algorithms for OTF initialization worked. “When I got the OTF working, the heart was racing a bit. Timo (Allison) and I had been working on this for quite awhile. I was sitting at my desk and we had a base station in another part of the office. We both watched as I would press the button to break the initialization and restart it—and it was literally happening in seconds. That was certainly a moment.”
At the 1994 FIG conference, Steve DeLoach, a civil engineer and land surveyor who led the RTK development program for the U.S. Army Corps of Engineers, saw Trimble’s RTK system with on-the-fly initialization in action.
“A couple of Trimble folks came up to me and pulled me over to a demo with the system on a range pole,” DeLoach said. “They would place a coin on the ground, survey its location, then turn their head while others laid down several other coins next to it. Then the guy with the range pole would occupy each coin until he was satisfied he was on the original point—and 100% every time, it was on target. It made me smile then, and it still does.”
Survey equipment manufacturers realized that GPS and RTK would be an integral part of the future of surveying. Leica acquired the civilian GPS business from Magnavox as a basis for its entry into the GPS and RTK business.
With surveyors adopting the technology broadly, manufacturers made significant advances in ergonomics, integration and miniaturization of the GPS receiver.
“Most, if not all users of the first RTK system that used known point initialization upgraded their receivers to dual frequency and the RTK-OTF capability because of the huge productivity gains it delivered,” Nichols said.
Ergonomics and integration improve field operations
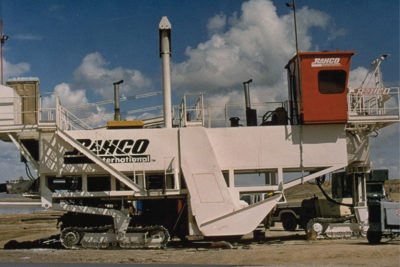
In an early example of RTK machine guidance, Rahco International put Trimble’s first RTK systems on a salt harvester to guide and control its movement. Source: Mark Nichols
In a parallel effort with the RTK advances, Trimble electrical and mechanical engineers miniaturized RTK hardware, better integrated system components, and added custom integrated circuit devices used to track GNSS signals. They also reduced power consumption so lighter batteries could be used in the field.
“The key evolution was to put the GNSS receiver and antenna, the radio for receiving corrections, and the batteries into a single package eliminating all cables, except for connecting to the data collector, which meant that the surveyor was no longer attached to everything,” Nichols said. “This significantly improved the usability of the system.”
Many of these early ideas, described in the patent “Pole-tilt sensor for surveyor range pole,” helped plot a roadmap for RTK survey product evolution in the following years.
Improved latency and update rate opens applications
The early generation of Trimble RTK products had a position fix update rate of 1 hertz, with a latency of 1-2 seconds. The slow update rate and large latency made navigation to stake-out coordinates iterative rather than smooth. “Try navigating with a device that is telling you where you were two seconds ago,” Talbot said. “It’s tricky.”
Trimble quickly realized it could enhance the user experience by increasing the position update rate and decreasing latency, which would open up a vast array of new applications in machine control and robotics in the years ahead.
Many hardware and software efforts came together in the Trimble 4800. With all rover components mounted on a carbon-fiber pole, the system provided a far more ergonomic configuration than earlier backpack-mounted products and became the form factor for future survey rovers from all manufacturers. In addition, solution latency was a fraction of a second, with an update rate of 5 hertz, and the system could operate up to 15 kilometers from the reference station.
“It really looked very smooth,” Talbot said of the 4800. “It was a quantum leap.”
Tide measurement benefits from RTK
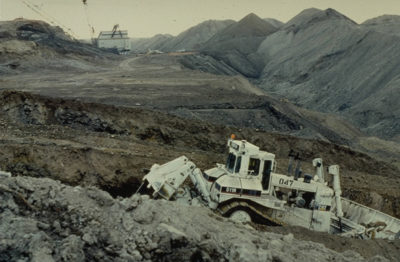
In the 1995-1996 timeframe, GPS grade control was used on a dozer at Black Thunder Coal Mine in Wyoming. Source: Trimble
In June of 1994, DeLoach worked with NOAA to operate the Corps’ prototype OTF-RTK system on an offshore buoy on the Bay of Fundy in a project with the University of New Brunswick, the Canadian Hydrographic Service and Canadian Coast Guard.
The algorithms developed during this project served as the basis for GPS tides and were incorporated into the Corps’ hydrographic surveying programs, described in DeLoach’s technical report “A Project to Determine Tidal Datums with the Global Positioning System.”
By 1997, the first permanent RTK network was implemented by Brian Shannon, a research engineer with the Corps’ Topographic Engineering Center. This network was for the Corps’ Jacksonville District to position vessels horizontally and measure water surface elevations for the Kings Bay entrance channel. By 1998, almost all Corps vessels and dredging operations had transitioned to RTK GPS.
Precision improves agriculture
RTK also made revolutionary inroads in agriculture. In the mid-1990s, John Deere and NASA’s Jet Propulsion Laboratory (JPL) started using GPS to enable precision agriculture.
The differential correction services provided by the Corps (Coast Guard beacons), Omnistar and Racal—and later the Wide Area Augmentation System (WAAS)—made it possible for the agricultural industry to apply GPS to yield monitoring and tractor guidance with submeter accuracy, setting the stage for future adoption of RTK in the agricultural industry. Such information helped farmers allocate future resources and determine which hybrids and management practices were most productive.
John Deere, in conjunction with Stanford University, pioneered early developments applying RTK to automatically steer tractors. In parallel, commercial GPS providers such as Trimble and the start-up company Novariant developed autopilot systems to retrofit existing tractors in the field. RTK was critical for steering tractors accurately enough to operate in high-value crops.
RTK-assisted guidance of tractors along regular patterns in open-field environments was yet another step towards the far-more complex task of controlling self-driving cars.
Standardization, new systems and signals provide common benefits
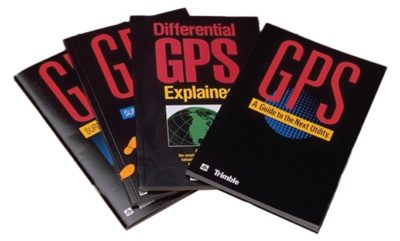
In the late 1980s, company founder Charlie Trimble was already describing GPS as the “next utility.” The advent of OTF-RTK enabled many high-value commercial uses of GPS to be realized. Source: Trimble
By the mid-1990s, several companies offered RTK products, each with its own proprietary reference station correction protocol, which limited interoperability when surveyors worked on construction sites or used public base stations as a service. “In many instances two or more reference stations had to broadcast proprietary corrections over a single site in order to allow rover equipment from multiple vendors to operate,” Talbot said.
Trimble, which used the Compact Measurement Record (CMR) format, recognized there would be a common benefit to customers and manufacturers in supporting a common reference station protocol. This was facilitated through the Radio Technical Commission for Maritime Services, Special Committee 104 (RTCM-SC104).
Trimble and other manufacturers supported the effort to develop a common interface, which was widely used from the late 1990s, with revisions for new satellite systems and signals coming along over the next decades, and described in a on Navipedia.
Surveyors the world over have enjoyed the great gift of free GPS signals from the United States, and with additional constellations, capabilities would further increase. The Russian counterpart GLONASS had limited satellite availability during the 1980s but towards the middle of the 1990s reached completion. “Trimble rolled GLONASS signal tracking capabilities, developed some years earlier, into its RTK product offerings,” Talbot said, “and this boosted RTK availability and accuracy.”
RTK enables machine control
One of the first uses of RTK for machine guidance/control was on a salt harvester as a part of a system developed by materials handling company Rahco International. “This was an RTK system without OTF,” Nichols said.
The ability to deliver centimeter-level positions with low-latency and high update rates made many other applications of the technology possible, as described in the patent “Centimeter accurate global positioning system receiver for on-the-fly real-time kinematic measurement and control.”
Around 1995, Trimble started developing a hardware product suitable for machine mounting. One of the biggest challenges was ruggedizing and shock-mounting the GNSS antenna and receiver. At this time, discussions had already started with Caterpillar, which led to the formation of the Caterpillar/Trimble joint venture. Soon, blade-mounted GNSS equipment was offered for bulldozers, enabling the best possible accuracy by directly measuring the blade position.
“The user interface provided the machine operator with a video-game-like experience that allowed them to grade to the design, free from string lines or survey stakes,” Talbot said.
Subsequent products integrated automatic hydraulic blade control for dozers and graders. Excavator bucket guidance was particularly successful. One benefit of the Caterpillar/Trimble joint venture was that it enabled customers to purchase machines with factory fitted GNSS hardware.
Virtual Reference Station (VRS) technology delivers benefits to governments
In 1999, Trimble hired Steve Berglund, previously president of Spectra Precision, as CEO, and in May 2000 announced it was acquiring Spectra Precision. This acquisition brought with it geodesy/mathematics experts Dr. Herbert Landau and Dr. Ulrich Vollath, and the software development team from the subsidiary, Terrasat, in Munich. The Terrasat facility went on to become the center for high-precision GNSS algorithm and software at Trimble.
Terrasat pioneered Virtual Reference Station (VRS) technology, which involved installation of a permanent network of reference GNSS equipment across regions, states, and countries, typically by government or large organizations. Data from the network was then massaged within a centralized server and transmitted as localized corrections for RTK rovers operating within the network. The VRS corrections largely removed satellite orbit and clock errors plus atmospheric errors across the network.
VRS networks were installed in many regions of the world. Forward-thinking government authorities saw the benefit of switching from maintaining aging geodetic ground mark networks, instead opting to deliver homogeneous VRS/RTK corrections to surveyors and construction firms.
VRS-for-RTK offered users significant advantages. “They didn’t need to own, set up or protect their own reference station equipment,” Talbot said, “which effectively cut the RTK system cost in half.” More importantly, it eliminated a lot of time-in-field overhead just to get a project started and completed each day.
Also by this time, other manufacturers produced RTK equipment, and surveyors benefited from the price competition. The reduced RTK product prices sparked another wave of uptake of RTK survey equipment around the world, this time by many smaller survey firms.
Faster, lighter, lower-cost technology opens possibilities
Early GPS equipment had very limited computing power, which constrained the sophistication of processing algorithms. “Faster computers generally required large power supplies,” Talbot said, “and this wasn’t an attractive proposition for human-mounted RTK.”
Thanks to the advent of smartphones, the new millennium saw the availability of fast, lower-cost, low-power CPUs, which were incorporated into GNSS hardware. This improved computing power enabled new and more rigorous processing techniques, including faster ambiguity resolution and extended range of operation.
In the 2000s, new GNSS constellations came online, including the Chinese BeiDou system, part of a dramatic increase in satellite signals from 2005 to 2015, including the European Union’s Galileo system. The result: new sources of measurement and improved availability and accuracy.
Commercial manufacturers responded by progressively releasing new GNSS receivers supporting the ever-increasing constellations in smaller and lighter configurations incorporating technologies driven by the smartphone industry, such as WiFi and Bluetooth, which eliminated cables.
The addition of inertial sensors in smartphones and automobiles drove down costs and enabled cost-effective integration of GNSS and Inertial Measurement Units (IMUs). “The tight coupling of inertial measurements with GNSS measurements has made it possible for surveyors and other RTK users to work in even harsher GNSS tracking environments,” Talbot said, “as well as benefit from tilted-pole operation.”
Opening up Precise Point Positioning
Around 2005, Landau floated the idea of Trimble producing its own precise satellite orbit and clock information in real time. Up until this point, only the International GNSS Service and NASA generated post-processed precise GNSS satellite orbits.
Landau, experienced with orbit estimation during his academic life, saw that centimeter-level orbit and clock information in real time could facilitate Precise Point Positioning (PPP) by rover equipment. The VRS experiences demonstrated the potential of using a global network of reference stations to service an unlimited number of users.
A large engineering effort started in 2011 resulted in the Trimble RTX correction service, which was delivered by satellite and internet, and available globally in both built-up urban environments and open farmland.
“Farmers were the first users of the Trimble RTX service,” Talbot said, “and many farmers across the U.S., Brazil, Europe and Australia already used Trimble RTK steering guidance and control systems, such as EZ-Steer.” Open-sky farming was ideal for the Trimble RTX service since the first release required 10-20 minutes of convergence time to reach centimeter-level precision.
With expanded satellite constellations, densified reference station networks and recent advances in technology, convergence to better than two-centimeter accuracy is almost instantaneous, making the system suitable for the geospatial, automotive and construction industries.
SoftGNSS makes debut
For the best performance, RTK has always required specialized GNSS hardware with custom chipsets supporting multi-frequency, multi-constellation GNSS signals. With recent advances in technology in RTK, GNSS receivers can run entirely as software in smartphones or other generic computing devices.
Using a high-quality antenna to receive the signals connected to a smartphone, it is now possible to get RTK accuracy from a lightweight antenna and a smartphone. Trimble Catalyst in 2016 became one of the first commercially available software-defined GNSS systems with RTK, consisting of nothing more than a 300-gram (less than one pound) antenna and a smartphone.
Centimeters everywhere for everyone
After it released its first commercially available RTK product, Trimble envisioned delivering centimeter accuracy everywhere for everyone. The development of high accuracy global correction services with high integrity, such as the RTX service, has been critical to fostering this vision.
Today RTK, enabled by the centimeter-accuracy global correction services, has truly become a utility. Beyond its birth in the surveying industry, it is enabling applications as diverse as agricultural and construction machine automation, outdoor augmented reality and semi-autonomous automobile navigation, such as with Super Cruise.
And in a full circle moment, the technology evolving to support these broader applications is likely to be used in survey products in the years to come.
Stacey Hartmann writes about surveying and geospatial topics for Trimble’s Geospatial division.
Link to part 1: https://amerisurv.com/2021/04/18/history-of-rtk-part-1-a-really-tough-problem-to-solve/
Link to part 2: https://amerisurv.com/2021/06/20/history-of-rtk-part-2-rtk-roots-run-deep/
Link to part 3: https://amerisurv.com/2021/08/15/history-of-rtk-part-3-everybody-wanted-it/