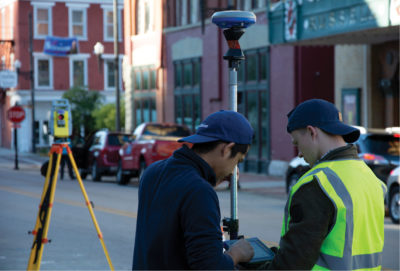
The normal challanges found in urban canyons bustling with RF interference, traffic, people, and structures are no match for Hybrid+ robust dual geodetic solution capability.
According to the futurist Daniel Burrus there’s a visible future if you know how and where to look. That’s precisely the warm and fuzzy I had while visiting with the forward thinkers of Carlson Software. As we approach the third decade of the millennium we find ourselves immersed in a new business climate bursting with opportunities driven by technology. The great recession has had a huge influence on our equipment lockers. Global engineering companies maintain large and amalgamated fleets of every color, brand, and type of measuring device available in every regional market. Regional mid-size firms are willing to invest in cutting edge systems but often carry a strong backlog of second string equipment assumed in mergers or local buyouts. The “small potatoes” firms realize their bang for the buck by purchasing the most cost-effective and compatible platform with their existing rig. And then there’s government procurement which undoubtedly will buy purple when you spec out yellow, blue, or green. The reality of our business is that equipment lockers look like boxes of Crayola crayons and our crews need to use every color to be effective. “Cross-color” compatibility requires the equipment manufacturers to develop in open-source by sharing their “nuts and bolts”.
Trains are “pains” to surveyors. Hybrid+ captures terrestrial shots with clear lines of sight and easily flips to GNSS collection when the train crawls by or worse yet stops in the siding.
That leads us to Carlson Software, Inc. with their flagship solution SurvCE/PC 6.0 data collection package. I was able to test drive the latest version on a Carlson RT3 ruggedized tablet running a Carlson CR+ Robotic TS (RTS) and a soon-to-be-released Carlson NR3 GNSS receiver interfacing with a local RTN. SurvCE naturalized these global components into a native system that seamlessly behaved as if it were proprietary and all one color. Carlson has the largest library of available drivers in the world. I’m sure there’s a few “secret sauces” in the industry but a glance at the available drivers list really does cover most every reputable manufacturer peddling survey gear. Manufacturers learned from the early auto industry that cross-licensing and open source strengthen an industry. Contemporary OEM’s of global/terrestrial positioning systems have traditionally subscribed to the principal and the result is a healthy market and innovative products.
The Hybrid+ solution is one of those innovative products incorporated into SurvCE/PC. Hybrid+ features a dual reading capability that synchronizes the terrestrial observation with the GNSS position at the user’s discretion. Selecting between measuring systems is accomplished with a simple toggle button on the screen and both are incorporated into the quality control component of Hybrid+. User defined tolerances set between GNSS and RTS measurements are analyzed by the software. The user is prompted to store, auto store, or in the event criteria are not met, the shot is flagged for further analysis by the user. This feature readily distinguishes stray reflector shots and poor GNSS conditions. The obvious benefit to having a combined rover and prism pole it that when one system is impaired by the “joys” of working in uncooperative environment, the other is seamlessly available by one simple click of a toggle button. Perhaps a less obvious benefit is that the
The front face of the staking screen offers a truckload of relevant data. GNSS satellite stats, heads-up tilt sensors, come/go/left/right pointers, cut/fill, point data, cardinal guidance, rod height, GNSS positional stats, and of course the Hybrid+ toggle near the upper left. Note the dynamic scale bar showing 0.2 ft as the shot is nailed down.
Redundancy between GNSS and RTS is obviously a huge quality control feature of Hybrid+ but which measurement is better? Hybrid+ offers the flexibility to choose based on the robust qualities of either system. Near the RTS, around canopy, and in urban canyons terrestrial measurements will, as expected, be much tighter than GNSS. The advantage of any brand RTS will radiate according to manufacturer’s specifications and well beyond ground zero at the setup. Nearing the effective limits of RTS is an environmental sweet zone where the resolution of both systems will yield similar statistics and the quality is equal. Beyond the reach of equality, the GNSS does the heavy lifting with the typical vigorous RTN statistics we are accustomed to seeing. Again, the user simply hits a toggle to select the result of either system as the stored measurement and the other as quality control.
In Resection, one button push combines the GNSS position precisely timed with the RTS result for robust real-time solutions. Any GNSS/GPS rover position can be a resection control point and the RTS position is precisely resolved relative to the datum pumped out by GNSS, Real Time Networks, or known benchmarks.
Hybrid+ is the ultimate free stationing solution. The RTS is no longer a slave to hard slab control networks, arbitrary assumed datum, or intervisible monuments. The RTS can be deployed at any convenient spot regardless of overhead canopy, aerial obstructions, and GNSS deal killers like urban canyons. The magic behind Hybrid+ is the rover’s ability to relate its precise geodesy to the RTS through every hole, crevice, cranny, or tunnel on the jobsite. Using the continual real-time position at the GNSS rover, Hybrid+ computes a geospatially accurate and statistically precise resection solution at the current RTS position. The GNSS constellation itself is the control monument and the rover antenna simply funnels the positional data through the Hybrid+ controller to the RTS. This truly liberates the robots from being autonomous hubs and employs the RTS as an active extension of GNSS and RTN networks.
Storing points in GNSS mode offers the positional statistics out front, the satellite stats on top, and the heads-up tilt sensors are clear and easy to read. Should GNSS be interrupted the RTS can be spun directly to the prism with the Hybrid+ toggle and search.
SurvCE also has some very nifty features worth a deeper look. My “short list” includes the new voice prompting for stakeout and instrument status. Voice prompting is exclusive to SurvPC 6.0 and allows users to keep focus on a point as well as keep an eye on traffic or heavy equipment. This seems like a “must have” for solo operators. The Tilt Correction routine uses the on board accelerometer and compass sensors to compute a point on a true vertical at the rover. The useable range is an extremely forgiving 15° to 20° out of plumb depending on manufacturer specs. This really speeds up acquisition and compensates for the jitters, sloppy rodsmanship, and shoehorning the shot around obstacles. I was impressed by the accuracy and repeatability of this correction. Web map overlays from Google, Open Street Maps, ArcGIS REST, and user defined Web Map Servers (WMS/WMTS/TMS) are now supported. Capturing data in real-time over good imagery is a windfall for quality control on a project site. GIS Inspector allows easy viewing of GIS attributes when selecting points in the map, and prompts for attributes when storing points from the map view. Surface Inspector compares plans against as-built elevation differences. The simplified routine helps to identify and express conformance concerns through as-builts in real-time on the job site. Relaying the as-built data through a connectivity package like Carlson Cloud gets those deliverables to the engineer at the speed of lightning.
The system is configured to aim precisely at the prism from the offset between the GNSS antenna. Cross-Check is required and was manually bypassed on the previous shot. The Cross-Check feature ensures robust and appropriate results prior to storing by comparing RTS and GNSS observations and user-defined tolerances.
As smart city technologies become reality our measuring systems will need to facilitate data collection in grossly congested environments of infrastructure, buildings, traffic, humans, and an ocean of RF noise. Carlson SurvCE/PC Hybrid+ appears to be a frontrunner in mitigating the environmental challenges associated with measuring the spaces where we live and work. Urban terrain is of course the Achilles heel of GNSS. The freedom to conveniently deploy the RTS and compute a resection from any convenient GNSS rover window opens up new opportunities in data collection. Hybrid+ is a smart tool for smart city capture with the capability to relate BIM data directly to geodetic datum and national or state plane coordinate systems. Just to add perspective to the aforementioned opportunities, Los Angeles World Airport hosts 84,557,968 annual passengers across 3,500 acres of RF saturated ground. The airport’s 2018 Capital Improvement Plan grosses out at $3,948,000,000. I read that as $4 Billion.
John Love’s resection methods described in Geodaesia circa 1688 (left). In 2018 Carlson Software combines GNSS and RTS with a simple toggle switch to perform real time GNSS/RTS resections (icon below).
That takes us to the Carlson Cloud command which is an Internet/cloud-based routine designed to easily facilitate sending messages, data files and crew locations between the office and Internet-connected field devices running Carlson SurvCE or Carlson SurvPC. Connectivity is an industrial milestone of biblical proportion like papyrus, the wheel, and the HP35. Carlson Cloud is leading the way with a robust security login including user, account, and company identification keys. Credentialed users are integrated into the connected environment and are identified on the grid. The chat tab connects users under the same company key with the option to select specific players from a drop list or the group at large. A “message area”
Voice command assists the solo operator in risky environments. The Hybrid+ resection freely allows the RTS to be set up at the most convenient places on a project. Both opportunities are safety multipliers on the jobsite.
Smart cities are fueled with data and we are primary suppliers. We work in a time when our skills and opportunities are very portable. Both expanding markets and a migratory workforce require great flexibility in choices of hardware, software, platforms, and systems. The bottom line is achieved by deploying any color combination of assets with every human resource at any spot on the globe. Carlson has taken a queue from the automotive industry and combined the best contemporary industrial components with Hybrid+ in order to leverage the strengths of all systems. The team at Carlson Software has once again pushed the technological envelope beyond industrial constraints and is redefining the way we work.