What often gets lost in the gloss of large construction projects are the small, precise elements that lead to the high-profile finish—the nitty gritty points and nuts and bolts that surveyors meticulously measured, set out and measured again to ensure buildings are straight, floors are level, tunnels are the right shape and railway lines are correctly aligned.
But surveyors are used to succeeding in the shadows—sometimes literally.
Nearly 40 meters below Auckland, the survey teams with Link Alliance have been guiding the successful build of New Zealand’s first underground rail network for the past two years.
The largest transport infrastructure project ever to be undertaken in New Zealand, the $4.4 billion NZD ($3.2 billion USD) City Rail Link (CRL) will build a 3.45-kilometer twin-tunnel underground rail link below the city center. The twin tunnels will vary in depth so two different construction methods are required: cut and cover where the tunnels are dug from the surface, and mined tunnels using either excavators or a 7-m by 7-m tunnel boring machine (TBM). Crews will also redevelop two existing stations (Mount Eden and Britomart) and construct two new underground stations (Aotea and Karangahape). When complete, the CRL will carry up to 54,000 people an hour, moving the equivalent capacity of three Auckland Harbour Bridges or 16 extra traffic lanes into and through the city at peak times.
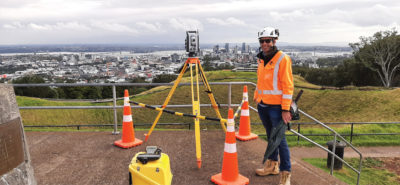
Establishing above ground survey control with a robust traverse network in preparation for the start of tunnel construction.
“As surveyors, we’re like the hunters and gatherers; we collect a lot of data and provide it to many teams,” says Sam Williams, surveyor manager with Link Alliance, a group of New Zealand and international companies building the CRL. “And it needs to be good data because the success of this entire project rides on the exactness of our survey points and measurements. We have to be right all the time.”
To Williams and his survey crew’s credit, their survey marks have been right 100 percent of the time since they first arrived on site in September 2019.
“With the accuracy, automation and user-friendliness of our gear, and the skills of our team, we’ve been able to work smoothly and quickly to keep everyone on track without sacrificing tight control, process or precision,” says Williams.
Under control
The first critical element they needed to get right was the primary survey control network, which was no easy feat given the project extends through three suburbs and principal construction would run through the heart of Auckland’s built-up central business district (CBD). Unlike with previous projects where tunnel survey teams have set up their own control networks, Williams wanted to establish a high-quality primary control network that could also be used for the entire project.
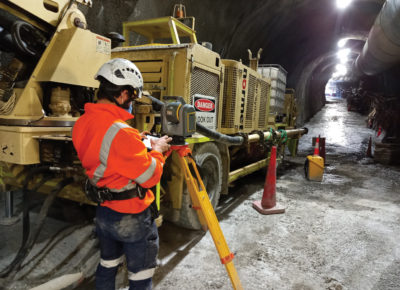
Using Trimble SX12 scanning total station instrument to measure as-built shotcrete thickness to verify the construction is meeting project tolerances.
Setting up on the summit of Mount Eden 4 km south of the CBD, Williams used Trimble R10 GNSS receivers to verify the Land Information New Zealand (LINZ) continuously operating reference station (CORS) at the port of Auckland and established that as his base station. He then carried out static GNSS observations on three existing LINZ datums and verified those accuracies. Satisfied with that foundation, he performed a series of four-to-six-hour observations with R10 receivers to extend the GNSS campaign to marks more relevant to the project. They established two new marks at each of the three project stations visible from the summit of Mt Eden—two of which were at heights of 10 stories and six stories. After the GNSS survey, Williams performed terrestrial observations with the Trimble S9 total station on the same intervisible marks to further improve the horizontal accuracy. He then input those measurements into Trimble Business Center (TBC) network adjustment software to more accurately compute each station’s coordinates, ultimately creating a primary network baseline precise to 1-2 mm.
For vertical control Williams performed a 10-km level run with the Trimble DiNi 03 level, measuring from the base of Mt Eden, down through each station and back again with an impressive misclosure of 4mm.
“The S9, DiNi and TBC network adjustment were game changers for this,” says Williams. “The long-range fine lock allowed us to measure and establish a 3-km baseline, in a built-up city environment, with a single prism at 1-2 mm accuracy. Pairing that with our vertical control results gave us the confidence that when we took that network down to street level and created secondary construction control for the guys on site, our tunnels and our stations were going to tie in perfectly.”
In the tunnels, the teams have been setting out targets at set intervals—every 80 m inside the TBM tunnels and 50 m inside the mined tunnels—and then build a secondary network off those to fill the gaps between and provide control on both sides of the tunnel.
With those primary and secondary control networks, Williams has maintained site control at the surface and in the tunnels at 3 mm or less.
Tracking the tunnels
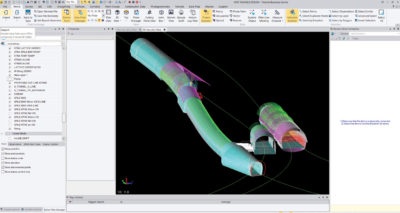
Trimble Business Center software was used to prepare the design data for field crew stakeout, and for QA/QC reporting during the construction process.
Whether setting out, confirming earthworks, guiding machines, marking bolt locations or capturing as-builts, life in the tunnels has been ruled by cramped quarters and “Hurry up.”
“Nothing advances without our survey support or confirmation, but mine tunnelling is very production focused so the tunnellers want you in and out as fast as you can,” says Darrell Wymer, Link Alliance’s tunnel survey manager. “Once an excavation or shotcreteing is deemed complete, we need to scan the cut and check that against the design model stored on our Trimble TSC7 controller to identify any underbreaks or overbreaks. From that scan we need to produce a point cloud to support the geologist’s geological mapping and create reports that show conformance to design for the construction, engineering and client teams—all in less than an hour. So, we’re under significant pressure to perform our work accurately without causing great delay to the tunnellers.”
They began to relieve some of that pressure in February 2021 when they acquired the Trimble SX12, a total station and scanner combination that can scan a full dome at 100 m with a point density of 0.1 m in 11 minutes, offers a 1.6-second total station measuring time in prism mode, and can pinpoint a 3-mm diameter spot at 50 m with its green, eye-safe laser pointer.
“With tunnels you need both total station and scanning functionality,” says Williams. “With the SX12, we have both in one unit and that alone saves us hours in the field because we can do our set outs, volume calculations and as-builts from one set up. And because the scans are automatically georeferenced, it saves us significant time in the office as well.”
The ability to perform multiple functions from the same set up has boosted their efficiency, precision and speed, particularly at Mt Eden and Karangahape, two of their busiest work sites.

The survey team using Trimble Access field software with the S7 robotic total station to guide and position rockbolt drilling machines.
For the Karangahape station tunnels, teams sunk a 25-m-diameter shaft 25-m deep and then tunneled 20 m east and west to provide launch points for excavating the station’s 278-m-long rail tunnels that include 203-m-long platforms. As the two excavators and road header advance, survey teams use the SX12 to guide the excavation, set out rock bolts, and confirm shotcrete layers.
“With the SX12, we can monitor the earthworks in real time and confirm excavation and shotcrete accuracy on the fly,” says Williams. “Once teams get to a certain advance point we set up and guide the last pieces using the instrument’s quick scanning and calculating functions in the TSC7’s Trimble Access software. When that’s done, we scan the finished excavation, compare it to the design model on our controller, and then scan the first layer of shotcrete. Then with Access software, we can use the previous excavation scan to produce a heat map that’ll indicate areas that don’t have proper thickness and they can top it up with shotcrete. It removes any need for post-processing in the office and keeps us moving.”
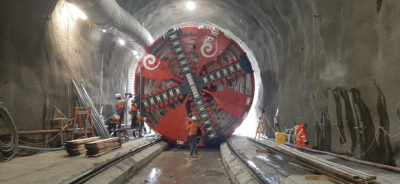
The survey team was instrumental to building the initial 50-m-long tunnel portal for the TBM and then ensuring it stayed on the right path during boring.
At Mt Eden, speed and agility have been particularly critical. As the first launch point for the 130-m-long TBM, teams first needed to create a 50-m-long tunnel to set the TBM on the right course for its 860-m-long journey to Karangahape station. In parallel, they began building three tunnels—each at different directions and heights—and constructing twin rail lines that will tie-in to an existing line. The functionality of the SX12 has enabled one, two-person crew to handle the aggressive workload.
“The ability to seamlessly switch between surveying and scanning has cut the time we need to be at the face checking and collecting data by 60 percent,” says Wymer. “We can collect a polygon scan of a tunnel face in about 2-3 minutes, and that’s including photos. That speed allows us to be so much more responsive.”
The confidence in knowing they’ve captured all the points they need at each set up has also been a boon.
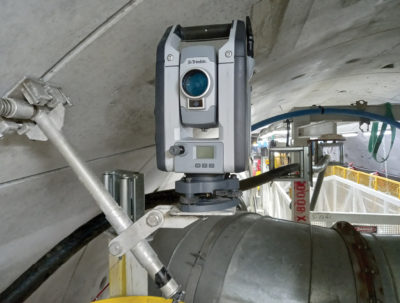
The Trimble S9 was used to establish survey control points for the TBM (tunnel boring machine) guidance system to ensure the tunnel was built in the correct direction, accurately.
“Usually, we’re about 10-15 m away from whatever we’re surveying,” says Williams “With traditional terrestrial total stations, we produce reports every 500 mm in chainage and every 300 mm of profile around the tunnel. Measuring each of those points manually takes a long time. With scanning, you pick up every surface in its entirety at 95 percent accuracy and you capture it all in minutes.”
All by design
Equal to the versatility and efficiency of their instruments has been their software functionality, particularly the TBC tunnel module where all the tunnel design and as-builting happens. Wymer has been using the specialized software to create three design profiles: one for excavation, one for the shotcrete lining and one for the final concrete lining—a process he needs to repeat for each tunnel section. All of those models are exported to the controllers for field crews to support the excavators and roadheader guidance systems and to guide, monitor and verify all the construction work like installing the reinforcement layers.
And sometimes, because of the dynamic nature of the tunnels and the geologic composition of rocks, Wymer’s had to be ready to respond to urgent requests for design model changes.
“There have been times when they’ve hit bad rock and the geologists have called for a design change,” says Wymer. “That means we have to generate a new design by the time the next cut is complete. On a good day we may have six hours to make changes to the profile and adjust bolt positions but if the call has been made overnight, we’ll often only have an hour to turn it around. With the scan detail and the automation and bulk data import features in TBC, we can meet these tight timelines so crews can keep working at speed.”
Working in dark isolation can make it difficult to see the light at the end of the tunnel but crews received their first validation that the CRL is on track on Oct. 16th when the TBM broke through at the Karangahape station site—right on target. It was a significant milestone and nod to Williams and his survey crews, giving them the confidence that their process, precision and tight control will serve the team well in their drive to complete the project by 2024.
“I’ve never been on a project of this scale, for this length of time and not had some sort of survey incident,” says Williams. “That’s a great testament to our team and our technology.”
It’s also a testament to survey crews who sweat the small stuff to achieve a big reward.
Mary Jo Wagner is a Vancouver-based freelance writer with 25 years experience in covering geospatial technology. She can be reached by phone at: +1 604 221 4583; or e-mail: mj_wagner@shaw.ca