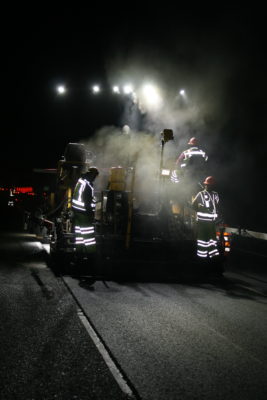
Knife River paved about a mile and a half of one lane per shift. The company dealt with a fairly narrow production window due to the amount of traffic on that particular section of I-5—about 5,000 cars through the work zone each night.
If the Jeopardy answer was: “The only continuous U.S. Interstate highway that touches the borders of both Canada and Mexico,” the answer would be: “What is Interstate 5, Alex?” Stretching nearly 1,400 miles, I-5 is the West Coast’s primary north-south artery running through California, Oregon, and Washington. Serving some of the U.S.’s largest cities, including Seattle, Portland, Sacramen to, Los Angeles, and San Diego, the highway handles as many as 300,000 vehicles per day–up to 35,000 of which can be trucks hauling freight.
So when a 12.5 mile section of the highway south of Portland, Oregon, recently underwent a repaving, the sense of urgency to get it done quickly–and with a high level of quality–was palpable. To improve the compaction facet of the paving operation, the Oregon Department of Transportation (ODOT) has increasingly demanded that its contractors employ Intelligent Compaction (IC) technology and this project showed why. The use of an IC system on each of Knife River Corporation’s four rollers, coupled with an integrated asphalt paver control system, and an ability to remotely monitor performance via a connectivity solution, produced some impressive results. The best example of that? A section of I-5 so smooth it had ODOT questioning the accuracy of their instruments–overall, an intelligent choice on many levels.
Taking the Next Step
Headquartered in Bismarck, N.D., Knife River Corporation (KRC) strives not only to provide the highest quality product possible, it also works to ensure its customers’ needs are met at every juncture. So when ODOT built the use of IC technology into the bid for the I-5 repaving project–part of a larger, nationwide DOT trend in this direction–KRC recognized it for the “next step” technology that it is, and won the bid.
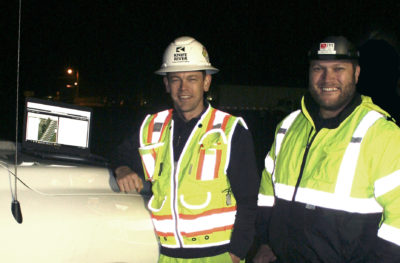
Monitoring the I-5 data are (left) Brodie Harvey, Knife River Corp. project manager, and (right) The PPI Group’s Richard Hill, paving/construction sales specialist.
“ODOT didn’t just recommend that we use IC, they made it a pay item,” said Brodie Harvey, KRC project manager. “Simply put, in order to get paid we had to use that particular technology. In addition, we needed to achieve a certain percentage of roller coverage every shift in order to avoid penalties. We hadn’t used IC prior to this project, but we recognized the direction this industry was taking with regard to the technology. Several of our team members attended ODOT sponsored training on the use of intelligent compaction in the time leading up to the construction season. We knew that ODOT had some high profile projects out there and felt that there was no better time to get on board.”
Started in Spring of 2017, the I-5 project called for the replacement of badly worn pavement on a 12.5 mile section of I-5, between the towns of Woodburn and Wilsonville, about a half hour south of Portland. That work is part of a larger overall project that will see the repaving effort stretch from Portland southward to the town of Albany–70 miles of new asphalt in both the northbound and southbound directions. “This section alone will involve placement of about 60,000 tons of asphalt,” said Harvey. “We are milling down two inches to the existing PCC pavement, then replacing that milled area with two inches of a new dense graded mix.”
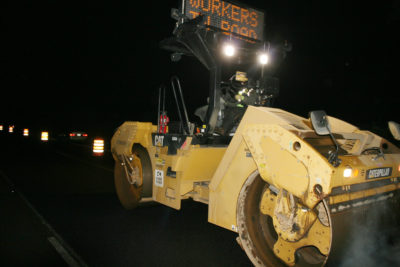
Designating start/stop points using landmarks such as signs or structures is virtually impossible in nighttime paving. Using IC, the operator always has both past and current position available on the screen.
Roads Are Getting IC
To make the move over to the new technology, KRC’s team met with representatives from the Portland branch of The PPI Group, a Topcon Solutions Store. Working with Richard Hill, PPI’s paving/construction sales specialist, KRC arranged to have an IC system installed on each of the rollers slated to work on that I-5 job.
“We are running four rollers out here,” said Harvey. “At the front, working directly behind the paver, we have a breakdown roller that is making four passes. That is followed by two intermediate rollers and a finish roller. We’ve worked with The PPI Group for some of our other paving systems–including the Topcon System 5 that is being used on the I-5 job–so we knew the level of support we would get during this critical transition to the new technology. More importantly, however, based on past experience, we knew Richard and PPI would be there long after the sale, and that’s already been proven.”
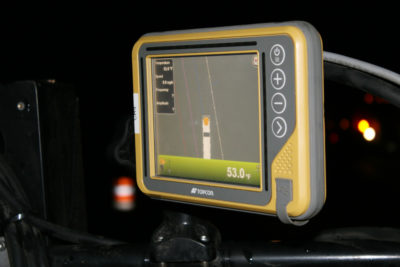
Here the front sensor temperature (sensors are located on the front and rear of the roller), is indicated on the screen’s bottom toolbar. Having mat temperature info readily available is invaluable in avoiding over- or under-compacting.
From the perspective of ODOT and the many DOTs who have also embraced the technology, the case to be made for IC is strong in many areas. They feel that, with IC monitoring a company’s rolling patterns and passes, contractors will be able to produce a better quality, more uniform, more economical product; that problem areas can be more easily identified and resolved; and that the data gathered through the IC process can be archived and re-purposed in the future as part of either a forensic investigation or road rehabilitation. Without even knowing it, KRC had arrived at what Topcon calls “The Intersection of Infrastructure and Technology,” a conceptual crossroads at which Topcon provides the advantages and knowledge–the solution, if you will–needed to harness technological innovation in order to increase productivity and profitability.
“Having accepted that IC was a pay item for us, we quickly saw the potential benefits it could bring to the table,” said Harvey. “The solution we chose, the Topcon C-63 Intelligent Compaction System, was extremely easy to grasp,” said Harvey. “I first spent about a day with Richard, learning how to set up the system and gain a comfort level with it. Then I tried it without his input on a non-contract required section of pavement and was easily able to get it to run on my own. Richard still stayed out with us for the first three nights of actual onsite use to make certain everything worked according to plan.”
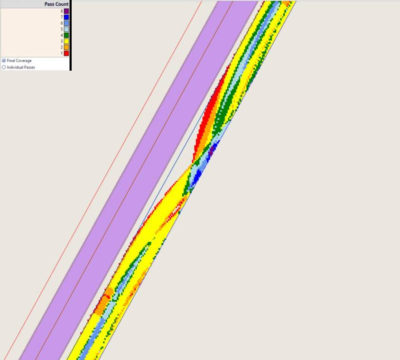
The as-built roll pattern of a single intermediate roller where a portion of the high side was being missed by an inexperienced operator. The KRC crew used this data to aid in the training of that operator and improve consistency of roll patterns.
Paint by Numbers
To those unfamiliar with the concept of intelligent compaction, it generally refers to the compaction of road material–soil, aggregate base, or asphalt pavement material –using vibratory rollers equipped with an integrated measurement system. The key components of KRC’s Topcon C-63 system include: an MC-i3 GNSS receiver; two temperature sensors; an accelerometer; a pair or antennas (a Topcon PG-S1 antenna for GNSS reception, and another cellular antenna for remote monitoring via Sitelink3D); and a GX-60 control box and screen. The goal is for KRC’s rollers to monitor compaction in real-time and, when needed, use those integrated measurement/documentation/control systems to make necessary adjustments to the compaction process.
“On the I-5 project, intelligent compaction actually began with a test strip at the beginning of the job,” said PPI Group’s Richard Hill. “KRC, and Materials Testing & Inspection (MTI) of Tigard, Ore., determined how many passes it would take to get the densities needed to meet ODOT specs. With that determined, we dialed that info into the C-63 system to tell each roller operator how many times they needed to target a specific area. Although the technology is complex, the idea behind it is fairly simple. Every time one of KRC’s roller operators makes a pass, the unit records it and the color changes on the C-63 screen–that allows him or her to see where they’ve been, where they need to go and how many passes they’ve made in that location. A lot of operators call it `coloring the screen’ or `painting by numbers.’ The bottom line is they have a verifiable way to see where they started and monitor their progress–a real asset when paving at night as they are here.”
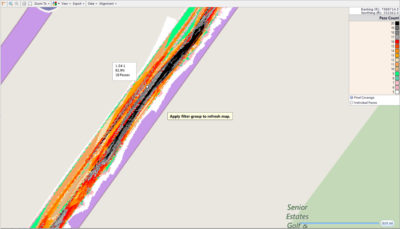
Composite (four rollers) as-built roll pattern. More passes = darker color, less passes = lighter color. The white dot is the location of a nuclear density test with a 92.9% value.
Because the temperature of the mat during compaction is so critical, front- and rear-mounted temp sensors continually measure surface conditions and display that number at the bottom of the GX-60 screen. “In the past, we had to use a heat gun to get those temps,” said Harvey. “And because those instruments are usually not calibrated, their accuracy was always questionable. That doubt has been eliminated. In addition, since we know the temperature ranges in which our compacted effort needs to be, our roller operators can watch those ranges. Often, if the finish roller is getting too cold, he’ll come out and push the other rollers forward so he can stay within the necessary temp range. That’s a huge benefit to quality and productivity.”
Solid Coverage
From a data gathering perspective, the Topcon IC solution breaks down the job site into 20 cm X 20 cm grids. Every time a roller hits one of those squares, the pass count, temperature, and a verification of whether or not the operator was using the vibratory unit in the roller, are all recorded. “That’s where percentage of coverage comes into play,” said Harvey. “We want to make sure we hit each one of those grid squares a pre-determined number of times in order to satisfy those criteria and avoid coverage penalties.”
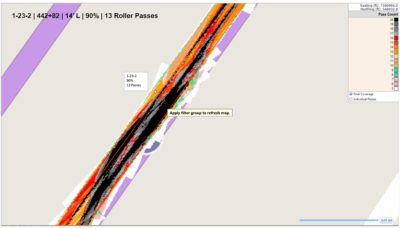
Composite (four rollers) as-built roll pattern. More passes = darker color, less passes = lighter color. The white dot is the location of a nuclear density test with a 90% value. KRC used the IC data + Sitelink3D to improve consistency of roll patterns.
In addition to accurate pass count and position, KRC’s operators also have the benefit of being able to monitor mix temperature and stiffness. All this data is continuously updated though the Sitelink3D Enterprise solution where real-time progress is both displayed for viewing and saved for future reporting. According to Harvey, that remote accessibility has proven invaluable throughout the I-5 project.
“I can monitor all these rollers on my laptop in real time as they are working. I can see their pass count; if necessary, I can control their screen, change their settings, modify the pass colors, etc., through a secure log in. This feature was ideal during the early phase of our IC implementation when Richard needed to monitor settings for us as we got familiar with the technology. I can’t overstate the fact that PPI Group’s customer service has been consistently excellent–Richard has been a key part of the team since we started.”
Nighttime Progress
As mentioned, the actual paving process involved putting down a single 2-inch lift of asphalt during nighttime closures. To make that happen, two of three lanes were shut down each night from 9:00 p.m. to 5:00 a.m. to make two lanes and the shoulder available for equipment, material delivery and workers. According to Tyrone Belgarde, KRC’s project superintendent, ODOT also demanded that they use a material transfer device to get asphalt to the paver.
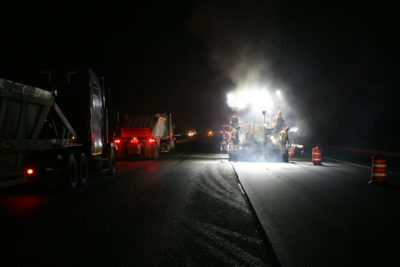
Knife River paved about a mile and a half of one lane per shift. The company dealt with a fairly narrow production window due to the amount of traffic on that particular section of I-5—about 5,000 cars through the work zone each night.
“We chose to use belly dumps and the windrow approach,” he said. “So we are grinding down to concrete, then we have a group up front that is checking for delamination or any other issues that need to be addressed before we cover it up. This project is a bit different in that, unlike most projects in which trucks are brought in after the paver, we are bringing them in before the work zone via our dead lanes. While that has caused some concern for our operators to have trucks continuously running by them, it has actually worked out well. The dump man–wearing a `halo light’ for easy identification by the trucks–has the belly dumps drop material in windrows and meters how much material goes on the ground as they travel forward. At that point, the windrow machine picks it up, remixes it somewhat as it comes up the elevator, then drops it into the hopper for augering and lay-down. We are paving about a mile and a half of one lane per shift; that’s about 2,000 tons per shift.”
Reporting for Duty
While the roller operator benefits greatly from what IC brings to the machine, the value of the data gathered via IC might be where the real advantage can be found. According to Harvey, a key benefit is using the solution to maintain a high level of confidence with the project owner, in this case, ODOT.
“In a sense, we use it to give ODOT peace of mind that their investment is paying off,” he said. “They are able to check project status, run reports, and so on–that’s huge. In addition, I spend one to two hours each day downloading the files, analyzing the data, and sharing the info with our crews. Based on data from the C-63, I send the superintendent and shift foreman a daily email which summarizes the results of our last shift. We are able to review all of the IC data for the exact location of each density shot taken on the project. We can now determine, with much more confidence, the cause of any low-density test values and react quickly to improve our results.”
Impressive Smoothness
While efficiency and information sharing are undeniably solid benefits, any paving operation’s success is ultimately determined by smoothness of the ride. In that regard, says Harvey, efforts on the I-5 project did not disappoint.
“When ODOT came out to check one of the sections we had already completed, we got some of the lowest IRI numbers they’d ever seen,” he said. “In fact, the numbers were so low there was concern that the profilograph, which had a new lasering system installed on it in the off-season, was not working properly. So they recalibrated the device, ran the road again and got the same numbers. This is a single-lift project, yet they got numbers in the low 20s–similar to what you would get with a three- or four-lift job. That told us that all our decisions–including the use of IC solution, the Topcon Paving System 5, Sonic Tracker II units and MOBA IR sensor on our paver– collectively, have helped this project move along the way it has.
“As a company, we like to think that the more info you have, the better decisions you can make. Because the intelligent compaction system from Topcon gives us so much valuable info, it’s really changed the way we think about compaction.” This portion of Knife River’s I-5 project wrapped up in late October.
Larry Trojak of Minnesota-based Trojak Communications is a freelance marketing content specialist. He writes extensively for the geopositioning, utility, aggregate processing, recycling, construction, and demolition markets.